Molybdenum Electrode Glass Melting Furnace
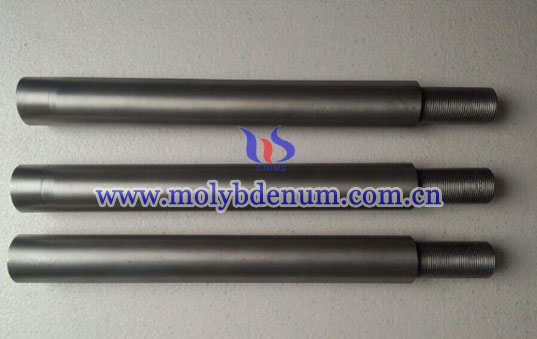
Many all-electric glass melting furnace and flame-glass melting furnaces use molybdenum electrodes. Mainly because molybdenum electrodes are widely used in melting soda lime glass, with a high temperature and surface current density, and using temperature can up to 2000 ℃.However, the proper use and performance of molybdenum electrodes are important factors for glass manufacturing and prolong the life of the glass and melting furnace.
After the study found that the greater surface current density of molybdenum electrodes, the loss will faster. In the glass melting furnace, molybdenum electrode surface current density in 1.0-0.7A/cm2 was moderate, but when the furnace require a higher quality of glass and longer electrode life, should adopt a lower surface current density. Molybdenum electrode surface current density the highest should not be greater than 2A/cm2.
Impurity content ratio of molybdenum electrodes, forged density level and density uniformity is the most important indicator of its quality, while its impurities and density will affect the preparation of the glass. First, the impurities main affect the service life and transparency of the glass, as well as the service live of glass melting furnace and molybdenum electrodes. The iron, nickel and other metel compounds which contain impurities the melting point of them is much lower than the melting point of molybdenum and glass, so these impurities will melt into the glass and it will cause early erosion by glass to molybdenum electrodes. So the glass transparency is poor, besides it will cause melting furnace failure and molybdenum electrodes are also easy to break.
On the other hand, forged density of molybdenum electrodes is an important factor for produce glass bubbles. Density distribution mainly refers to the radial distribution. Generally, section density is less than center portion of the electrode and the difference should be controlled at about 2-5%. The excessive difference is likely to cause molybdenum electrode erosion, and then later a lot of molybdenum particles get into the glass, causing glass turn to gray. On the other hand, longitudinal density distribution uneven will cause little micro DC potentiometer which is easy to produce micro-bubbles in the molten conductive glass.
Therefore, the correct use and excellent produce of molybdenum electrodes for the performance of glass and protective glass melting furnace is an important factor.